Delivering medical devices that meet the needs of countries and regions with the sense of pride and responsibility of a global corporation
In 2021, Sysmex launched a new compact instrument product for the hematology field. Takahito Mihara, development team leader, explains the background to its development as follows:
“The compact device that we developed is targeted at small- and medium-sized hospitals and clinics. In Asia and Latin America there are many small- and medium-sized hospitals and clinics, but most had little space available for a testing instrument, making installation difficult. The places that patients went for tests were small- and medium-sized clinics where their doctors practiced. If we could make a product with an assurance of the accuracy and stability of data provided by Sysmex testing instruments, but which could be installed in a limited space, we could provide the people in local areas with the opportunity to know about their health condition. By doing this, we thought it would be possible to contribute to improving access to medical care in emerging countries. It was a medical device that we felt had to be widely adopted because of its connection to people’s lives.”
There was another major mission in the development of this product. We were aiming to reduce environmental impacts not only in logistics and other processes within Sysmex, but also when customers use our products. As a global company delivering products and services to over 190 countries and regions worldwide, in addition to assuring the high quality required for a medical device, we accepted the challenge of creating an environmentally friendly product design.
Experiencing customers’ situations at first hand produced a strong sense of mission
Existing compact models had played an important role for our customers for a long time. As this was the development of a new product after a gap, we started by thoroughly collecting information. In order to accurately understand the situation of clinics in emerging countries, we conducted needs surveys together with our sales representatives.
According to Mihara, “Not only sales representatives but also the developers themselves visited medical institutions, distributors, and subsidiaries in other countries to hear about their needs and points for improvement. We visited customers in India, Indonesia, Brazil, and Mexico to interview them in detail about issues they had experienced in testing and the functions they desired. We gained a lot from being able to observe at first hand the testing laboratories where Sysmex products were in use. We found out that, due to insufficient infrastructure in many emerging countries, it was difficult to call in maintenance personnel, and space for testing devices was not readily available. Experiencing what local situations were like, I keenly felt the need for a product to be robust, have low running costs, and good transportability. I think that this experience led to product development from the customers’ perspective and was a driving force in overcoming technical obstacles at the development stage.”
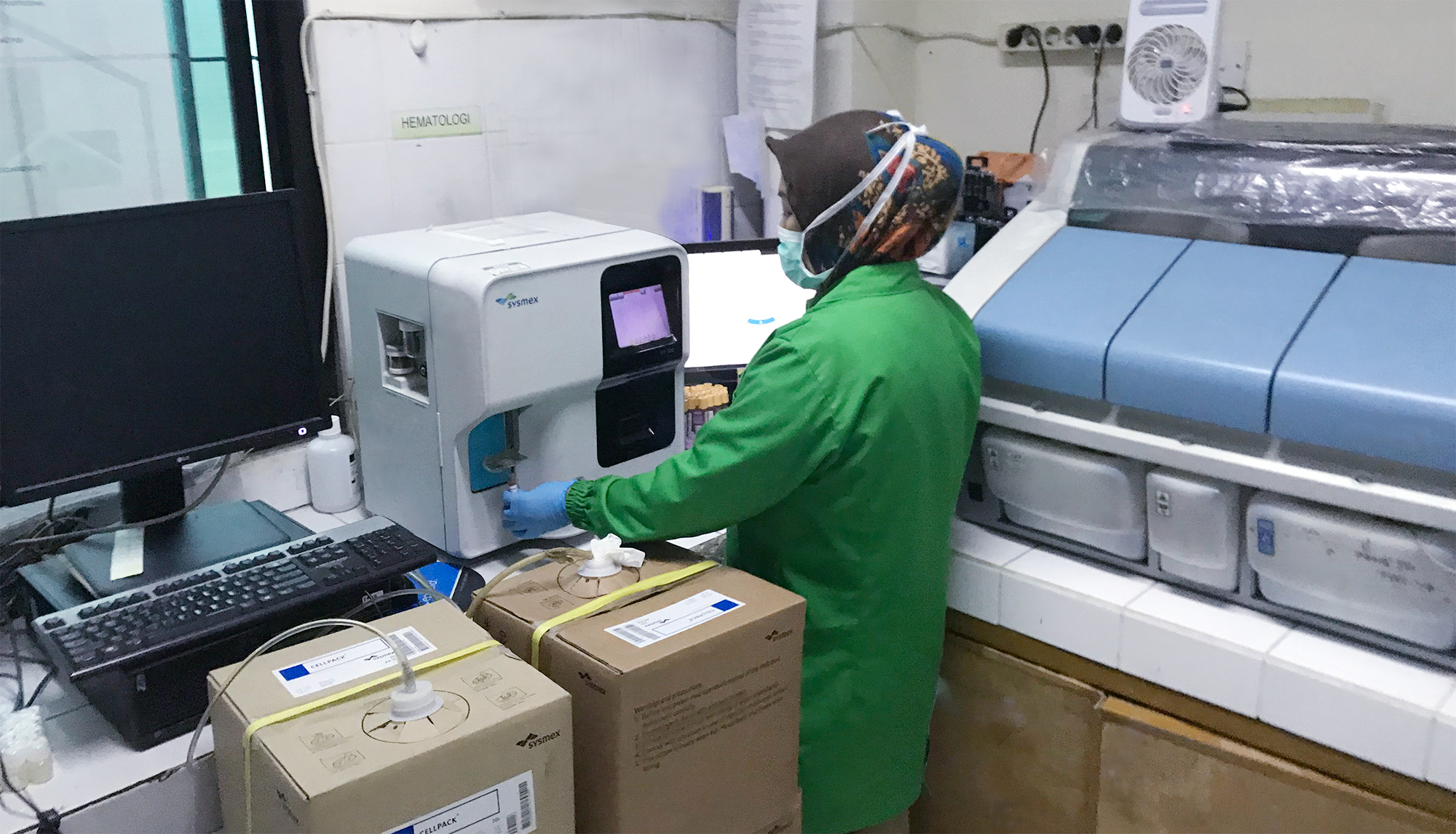
Testing lab visited in Indonesia
In addition, specific numerical targets were set for reducing environmental impacts. The challenging numerical targets adopted were reducing weight ratios by 30% and power consumption by 25% compared to previous models, with the aim of reducing CO
2 emissions and reducing water usage by 10%.
“To be honest, when I first heard the numerical targets for environment friendliness I wondered whether we could actually achieve them. But, at the same time, I strongly felt that, as a medical device manufacturer contributing to healthcare worldwide, it was our mission to accomplish the development of the product and fulfill our responsibility by carrying out the project for it. In the design, we made many improvements and modifications, but there was no going back because we had clear numerical targets from the beginning. We were able to forge ahead with no team member showing any compromise.”
Looking back, Mihara mentions that he had experienced improving the quality of existing products, but this was the first time for him to be involved in the development of a new one. He says that leading the development team while collaborating with other departments was a continuous learning experience.
“First, the team members and I set numerical targets for quality aspects. Since the reagents to be used were the same as for previous models, we focused on reviewing the measurement operation flow. It would be no good to have targets that were too low, but if they were too high it would negatively affect the team’s motivation. Through discussion within the development team, we searched for optimal targets.”
Innovative product bringing together all of our strengths, with an optimized overall balance
In consideration of customer needs and reducing environmental impact, we had discussions with other departments on the size and specifications for the design. According to Mihara, the hardest thing to do was adjusting the overall balance.
“The most difficult thing was to create an overall product design achieving a size and weight optimized for ease of use in clinical laboratories with no loss in the stability or reliability of measurement data and a reduced environmental impact. First, we aimed at a lightweight, robust device and focused on material selection and the basic design. Repeating experiments with various materials, we persisted until we achieved an ideal design. We studied three patterns of model simultaneously on a PC, with development team members suggesting improvements and modifications.”
“This was the first internal project to be carried out under consistent management across departments with the aim of developing a product that reflects the customer’s voice. Assigning project members from each department to the same floor allowed for daily discussion and led to highly active interdepartmental communication. We were able to identify improvements from various viewpoints early on and focus on implementing them quickly. By having members of the manufacturing and service divisions operate the prototype device from an early stage, both points for improvement and new ideas emerged. We received much advice on points that the development team had not noticed.
As there were conflicting opinions at times, we repeated experiments dozens or hundreds of times to find optimal solutions that everyone could agree on, and kept pushing ahead. By working together with other departments, we were able to view the product from multiple perspectives and make adjustments that achieved an optimal overall balance.”
As a result, improved stability and reliability were achieved for data with a small-size device. Also, reducing the amount of blood used from about 50 μL to 16 μL allowed the specification to be adjusted to one with less physical burden on patients. In addition, increasing throughput made it possible to report results to patients more quickly.
Improvements to make the device lighter and more compact achieved a size that was easy to install for small- and medium-sized hospitals and clinics. Previous testing instruments could only be started up after the arrival of medical staff at a clinic. Innovations in the specifications for the new compact instrument to improve usability allowed it to be started up automatically at specified times on specified days, helping greatly to raise efficiency in clinics. The team achieved a product that was beneficial for both medical staff performing tests and patients, by ensuring high quality measurements even in small facilities such as in clinics.
The numerical environmental impact targets specified for the project - reducing CO
2 emissions and water usage amounts - were successfully achieved, allowing an environmentally friendly product to be developed. It took just two years from initial development to launch. Completing it in such a short period of time by bringing together Sysmex’s strengths enhanced our ability to make rapid responses.
Mihara further says, “Through developing this product, we realized that aiming to reduce environmental impacts and responding to customer needs are the same thing. This development style did not follow precedent and through a pooling of the knowledge and technical skills that Sysmex has built up, I feel that we created a new type of innovation.”
Taking the lead in healthcare worldwide through environmentally friendly products
We have received feedback from customers who use this product that it meets their needs in terms of throughput, size, functionality, and usability. Their positive comments are proof that the product developed by the team has value for customers. Mihara says the following about product development:
“New product development is not only about creating a brand-new product. Development means understanding what customers want and creating high-quality products that meet their needs. As a leading company in the hematology field, Sysmex has a responsibility to achieve high quality and set challenging goals. Therefore, in the future, keeping abreast of the needs of healthcare professionals and patients, we aim to continue delivering products that customers can use with peace of mind. Medical devices with high quality and usability that are also environmentally friendly provide an added value that meets the needs of medical institutions and society worldwide. Going forward, we aim to further enhance our efforts in product development to incorporate this kind of sustainability perspective.”
Sysmex will continue its contribution to realizing a sustainable society through the development of environmentally friendly products and other initiatives that contribute to the environment.